Inconel Alloy 600
Table of Contents
1. Introduction of Inconel 600
Inconel 600(Alloy 600, or UNS N06600), is a strong nickel-chromium alloy. It has great resistance to oxidation, carburization, and corrosion.
This makes it useful in many industrial applications. Manufacturers commonly use this alloy in high-temperature settings and where they need strong materials. A popular choice in industries like chemical processing, aerospace, and power generation exists. Alloy 600 is a nickel-chromium-iron alloy that provides superior durability, especially in high-temperature environments.
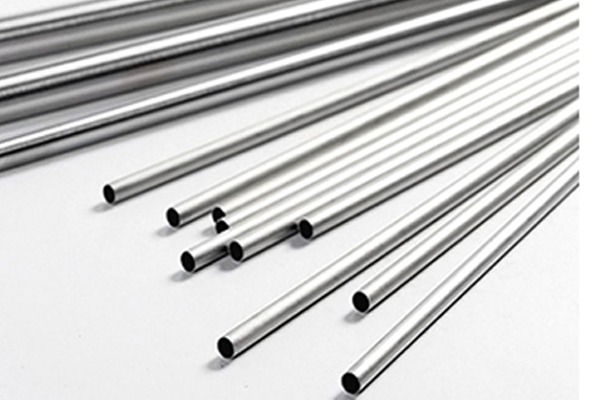
2. Chemical Composition of Alloy 600
Inconel 600 composition consists primarily of nickel, chromium, and iron, with small additions of other elements. Below is the typical chemical composition of Inconel 600:
Element | Percentage (%) |
---|---|
Nickel (Ni) | 72.0–76.0 |
Chromium (Cr) | 14.0–17.0 |
Iron (Fe) | 6.0–10.0 |
Manganese (Mn) | 1.0 max |
Copper (Cu) | 0.5 max |
Silicon (Si) | 0.5 max |
Carbon (C) | 0.15 max |
Sulfur (S) | 0.015 max |
Key Alloying Elements and Their Roles:
- Nickel (Ni): The primary element in Alloy 600, nickel imparts excellent resistance to oxidation, carburization, and high-temperature corrosion. It provides good strength and ductility, making the alloy suitable for high-temperature and aggressive environments.
- Chromium (Cr): Chromium enhances the alloy’s oxidation resistance and contributes to its resistance to corrosion in many acidic and alkaline environments. It also helps improve the alloy’s overall high-temperature stability.
- Iron (Fe): Iron is the basic component of the alloy. It adds strength and forms the base of the alloy’s structure. It helps to lower the cost of Inconel 600 compared to higher-chromium alloys.
- Manganese (Mn) improves the alloy’s resistance to oxidation and scaling at high temperatures. It also enhances the alloy’s ability to resist stress corrosion cracking (SCC).
- Copper (Cu): Copper enhances the alloy’s resistance to corrosion in some acidic environments and also improves its general toughness. Manufacturers keep the copper content low in Inconel 600 to avoid adverse effects at elevated temperatures.
- Silicon (Si): Silicon provides increased resistance to oxidation and improves the overall strength of the alloy at elevated temperatures.
- Carbon (C): Carbon helps to stabilize the alloy’s structure and improve its strength. Too much carbon can cause carbides to form. This can harm the alloy’s ductility and its ability to resist corrosion.
These elements make Inconel 600 a great material for uses that need high strength. It also has excellent oxidation resistance and durability in extreme heat and corrosive conditions.
3. Physical Properties of Alloy 600
The physical properties of Alloy 600 provide its versatility in various applications. Solid solution strengthening gives outstanding mechanical properties at both room temperature and elevated temperatures.
Property | Value |
---|---|
Density | 8.47 g/cm³ |
Melting Point | 1370–1425°C |
Tensile Strength | 80,000–120,000 psi |
Yield Strength | 30,000–60,000 psi |
Elongation | 30–45% |
Hardness (Rockwell B) | 85–95 |
4. Corrosion Resistance of Alloy 600 Material
Alloy 600 is highly resistant to corrosion, particularly in environments where resistance to stress corrosion cracking is critical. Its high nickel content makes it better for places like chemical processing and heat exchangers. These areas deal with strong chemicals and high heat. The alloy’s excellent resistance to oxidation and carburization makes it ideal for high-temperature applications.
One of the notable characteristics of Alloy 600 is its superior resistance to chlorine and chlorine-containing environments. This property makes the applications highly effective when users involve chlorine gas or other chlorine compounds.
Alloy 600 shows great resistance to chlorine gas and chlorine compounds. This makes it good for many chemical processes. Especially useful in making chlorinated chemicals and chlorinated solvents.
Key Applications in Chlorine-Related Industries:
- Chemical Processing: Alloy 600 is used in reactors, piping systems, and equipment that process chlorine and chlorinated substances. Its resistance to chlorination and chloride-induced corrosion makes it an ideal material for these environments.
- Metallurgical Industry: Manufacturers use chlorine gas to make metals like titanium and zirconium. It helps in producing titanium tetrachloride. Manufacturers often use Alloy 600 for furnace parts, piping, and heat exchangers.
- Waste Disposal: Waste disposal plants can release chlorine gas or chlorinated compounds. Alloy 600 is resistant to chlorine corrosion in these environments. This resistance helps it last a long time.
5. Heat Treatment and Processing
Alloy 600 can be easily heat-treated to optimize its mechanical properties. The alloy can go through different processes. These include annealing and solution heat treating.
These methods help achieve the right balance between strength and ductility. Also resistant to thermal embrittlement, this material makes a reliable choice in high-temperature environments.
Heat Treatment Process | Temperature Range (°C) |
---|---|
Solution Annealing | 1000–1100 |
Stress Relief | 750–900 |
The alloy keeps its strength and resists oxidation at high temperatures. This makes it good for heat exchanger tubing, reactors, and other uses.
6. Applications
Alloy 600 is widely used in several industries that demand high strength and good oxidation resistance at elevated temperatures. Notable applications include:
- Chemical Processing: Used in reactors, piping systems, and heat exchangers.
- Aerospace: Engine components and exhaust systems.
- Power Generation: Gas turbines, nuclear power plants, and heat exchangers.
- Food and Beverage: Heat exchangers in food processing.
Engineers often use Inconel 600 in high-temperature gas and steam applications. People know it for its great resistance to corrosion and high performance.
7. Comparison with Other Nickel Alloys
Inconel 600 is a popular nickel alloy. People often compare it to other high-performance nickel alloys like Inconel 625 and Inconel 718. Below is a comparison of Inconel 600 with these alloys to highlight their respective strengths and typical applications:
Property | Inconel 600 (Alloy 600) | Inconel 625 (Alloy 625) | Inconel 718 (Alloy 718) |
---|---|---|---|
Composition | Nickel, Chromium, Iron | Nickel, Chromium, Molybdenum, Niobium | Nickel, Chromium, Iron, Niobium, Molybdenum |
Corrosion Resistance | Excellent in oxidizing and carburizing environments, good resistance to chlorine and chloride-induced corrosion | Exceptional resistance to marine environments, highly resistant to pitting, crevice corrosion | Good resistance to oxidation and corrosion, especially in high-pressure environments |
Temperature Resistance | Excellent resistance at high temperatures (up to 1100°C) | Superior resistance to elevated temperatures, especially in extreme environments (up to 980°C) | Excellent at high temperatures, superior strength at elevated temperatures (up to 700°C) |
Mechanical Strength | High strength, solid solution strengthened | High strength, especially in severe environments | Very high tensile and yield strength, solid solution strengthened |
Applications | Chemical processing, heat exchangers, aerospace, high-temperature gas turbines | Marine applications, aerospace, pollution control equipment, high-stress environments | Aerospace, gas turbines, nuclear reactors, pressure vessels |
Weldability | Good weldability, suitable for high-temperature welding applications | Excellent weldability, often used in welded structures | Good weldability, used in critical welding applications |
Cost | Relatively lower cost compared to Inconel 625 and 718 | Higher cost due to molybdenum and niobium content | Higher cost due to the addition of niobium and molybdenum |
8. Inconel 600 Product Forms and Market Availability
Alloy 600 is available in a variety of product forms, including:
- Inconel 600 Round Bars: Commonly used in structural applications where high strength is required.
- Inconel 600 Plates: Ideal for manufacturing parts that require a good balance of strength and formability.
- Inconel 600 Pipes: Often used in heat exchangers, chemical processing applications, and other high-temperature operations.
- Inconel 600 Forgings: Used in critical components such as turbine blades, fasteners, and other high-stress parts.
The global market for Alloy 600 is strong. Key suppliers include Special Metals, Rolled Alloys, and Upmet.
They offer many product forms for different industrial uses. People often use these products in aerospace, chemical processing, and power generation. Their ability to resist high temperatures and corrosion is crucial.
SOUTHERLY ALLOY is a reliable exporter of Inconel 600 materials and products. We offer high-quality Alloy 600 round bars, plates, and pipes to customers around the world. Our extensive inventory and prompt delivery services ensure that industries relying on high-performance materials can easily access the materials they need.
9. Conclusion
Inconel 600 is a strong nickel-chromium alloy. Popular for its perfect resistance to oxidation, carburization, and high temperatures. Its chemical composition, which includes significant amounts of nickel and chromium, provides remarkable durability in aggressive conditions, such as chemical processing and aerospace applications.
Inconel 600 is a great choice for industries that use chlorine gas or compounds. It resists chlorine and chloride corrosion exceptionally well.
With its ability to maintain strength and integrity under elevated temperatures, Inconel 600 continues to be indispensable in various sectors. Products like Alloy 600 round bars, plates, and pipes are widely available. A strong supply chain makes sure industries worldwide can rely on this versatile alloy for their toughest needs.