1. Intro
This is a story about improving the hardness of nickel alloys. Last year, we received an order from a overseas customer, asking for Inconel 901 alloy plates with a hardness of 38HRC. According to our inquiry, the hardness of Inconel 901 super alloy is usually between 30 and 35HRC. Undoubtedly, a significant challenge awaits us.
After discussing with the engineer, we think that with the right process treatment, we can meet the customer’s hardness needs. So we decided to accept this order.
Even though this is a small custom order, we must consider the material’s weight. This will help us ensure that the final cut meets the size requirements. Based on the customer’s needs, the material weight is about 25 kg. However, to ensure easy cutting after forging, we decided the forging block should weigh 35 kg.
2. Starting from the source, request to improve hardness of nickel alloy
To make sure the hardness meets the standard, we have set strict rules for choosing raw materials. We ask raw material suppliers to provide materials that they have forged several times. This ensures their hardness and structure meet the needs for further processing.
The whole forging process takes a lot of time. This delays the delivery cycle and pushes back the customer’s original delivery date.
The multiple forging of the forging block requires the process of heating, forging, and annealing. The material is too light to set up a furnace by itself. Therefore, we must process it with other materials. This leads to an extended delay.
The delivery period of 10 days eventually experienced a delay of 10 days. After about 3 weeks, we finally got the forging block from the factory. The actual weight was 38.3 kg.
3. Hardness test and solid solution aging treatment
After receiving the forging block, start by conducting spectral detection and hardness test.
The spectral analysis results meet the requirements, and the only problem is that the sulfur content is slightly elevated.
The results of the hardness test are 32, 32, 34HRC, which is still a certain distance from the 38HRC required by the customer.
Next step, we will carry out solid solution treatment and aging treatment. According to the information consulted by the engineer, the following treatment plan was determined:
In making 901 cubes, we use artificial aging technology. This process heats the metal material to a specific temperature. This creates a strong hardening effect in the precipitates. This process significantly improves the hardness of the material, making it more wear-resistant and pressure-resistant during use.
After several days of adjustment and processing, we finally got the ideal hardness results. After the solution and aging treatment, we measured the hardness of 6 out of 8 workpieces. The results were: 39 HRC, 38 HRC, 38-39 HRC, 38 HRC, 40-41 HRC, and 39-40 HRC. These results fully met the customer’s requirements.
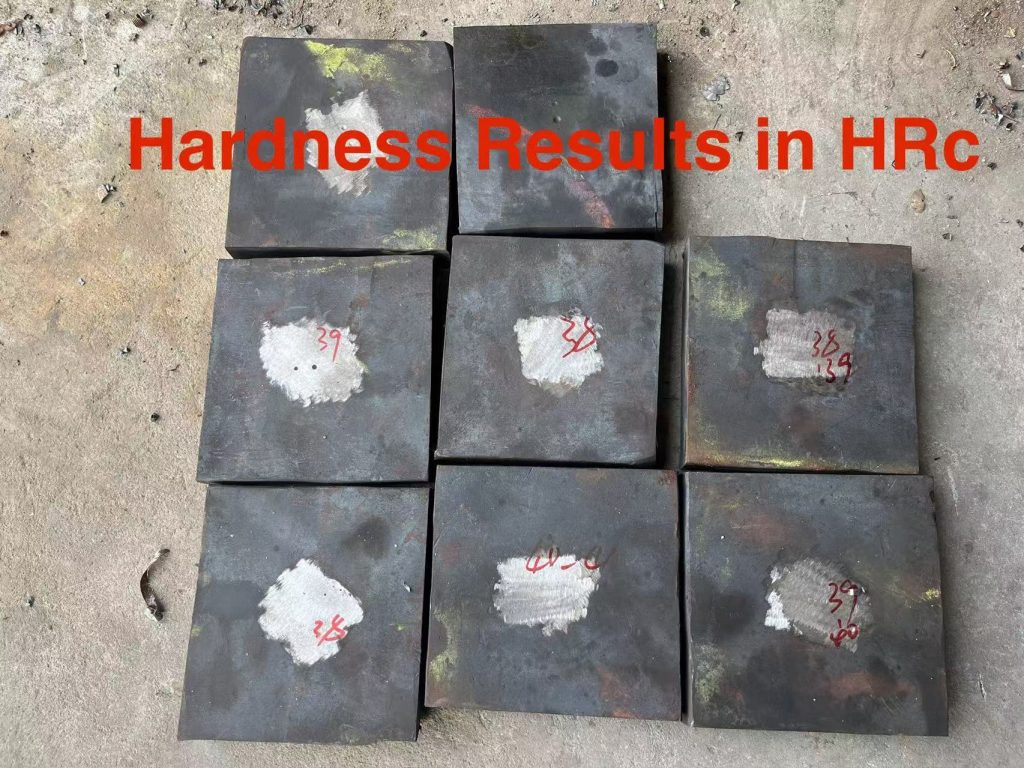
4. Subsequent cutting and surface treatment
Because the material is extremely hard, we cannot use traditional turning and sawing methods. Instead, we chose wire cutting technology. This method allows for precise processing and ensures the final product meets the customer’s size requirements. During the entire processing process, we also recorded on-site videos to ensure transparency and quality control.
Finally, the team finished the product after surface grinding. They delivered it to the customer by express delivery on time. After the customer received the goods, they were eager to start processing them. After some time, they told us they were extremely satisfied with the material.
5. Summary and reflection of How to improve hardness of nickel alloys
In this case, we used strict process control and made several adjustments. As a result, we met the customer’s hardness requirements and delivered smoothly.
Even with delivery pressure and technical challenges, we overcame difficulties. Our team worked together and improved technology to ensure product quality. Customer feedback also verified our efforts and dedication.
This experience tells us that when facing orders with special requirements, details determine success or failure. A careful process, good quality control, and clear communication are key to smooth delivery.
This experience has shown us how important teamwork is. Each member played an important role. The engineers improved the production process. The quality assurance team carefully checked every batch.
In conclusion, this successful delivery has pleased our customer and made our team feel proud. It serves as a reminder that with dedication, teamwork, and a focus on quality, we can overcome any obstacle. We are excited to use these lessons in our future projects. We believe we can keep meeting and exceeding our customers’ expectations.