What is Inconel?
Inconel (including inconel 600, inconel 625 ect.) is a registered trademark representing a group of austenitic nickel-chromium-based superalloys. These alloys are designed for extreme environments, capable of maintaining their strength and resisting oxidation and corrosion.
The most representative materials in the “Inconel” series include Inconel 600, Inconel 601, Inconel 625, and Inconel 718, each grade optimized for specific applications. These superalloys are mainly used in environments requiring high temperature and corrosion resistance. This article focuses on the unique properties of INCONEL 625 and its applications in various demanding environments.
INCONEL 625: Composition and Properties
INCONEL 625, also known as Alloy 625, is one of the most versatile and widely used Inconel alloys. Its chemical composition includes a high proportion of nickel (minimum 58%) and chromium (20-23%), along with significant amounts of molybdenum (8-10%) and niobium (3.15-4.15%). This unique composition gives INCONEL 625 its distinctive properties.
• Density of Alloy 625:
The density of alloy 625 is approximately 8.44 g/cm³, which is relatively high compared to other materials, contributing to its strength and durability.
• Hardness of Alloy 625:
Alloy 625 exhibits excellent hardness, with a typical Rockwell hardness of 30-40 HRC, making it suitable for applications requiring high wear resistance.
• Melting Point:
The melting temperature range of alloy 625 is 1290°C to 1350°C, allowing it to maintain structural integrity at high temperatures.
• Yield Strength:
The yield strength of alloy 625 is about 460 MPa, ensuring it can withstand significant mechanical stress without permanent deformation.
Applications of Alloy 625
Because of its unique properties, the applications including:
Aerospace:
Alloy 625 is used in jet engines and other aerospace parts. It can handle high temperatures and harsh environments.
Its high strength and resistance to oxidation make it a good material. It is ideal for turbine blades and also suitable for exhaust systems and other important parts.
Marine:
Its resistance to seawater corrosion makes it an ideal choice for marine applications, including submarines and shipbuilding. Manufacturers commonly use alloy 625 in marine hardware, propeller blades, and underwater communication cables.
Chemical Processing:
INCONEL 625 is used in chemical processing equipment. It can resist many corrosive chemicals. You commonly find it in reactors, heat exchangers, and piping systems that handle corrosive chemicals.
Power generation equipment
Uses it in nuclear reactors and other applications. High temperature and corrosion resistance are very important. Engineers use alloy 625 in steam generators, gas turbines, and other high-temperature components.
Bioenergy generation
Widely uses Alloy 625. Biofuels produce a lot of halides when burned. These halides can be very corrosive at high temperatures.
Alloy 625 has at least 58% nickel. This makes it resistant to halogen corrosion in these conditions. Therefore, it is widely used in bioenergy generation equipment.
Exhaust Waste Heat Recovery:
In boiler exhaust waste heat recovery, regular stainless steel pipes can corrode in high temperatures. However, Alloy 625 resists corrosion well in these conditions.
To save costs, manufacturers often use alloy 625 as a cladding welding material. It is used in boiler exhaust waste heat recovery. This helps improve equipment reliability, lower maintenance costs, and extend the life of the equipment.
• Welding Overlay:
Alloy 625 is more commonly used as a welding overlay in hot corrosion environments. In addition to recovering waste heat from exhaust, many industries use Inconel 625 as a welding overlay in various situations.
In the petrochemical industry, oil pipelines and valve fittings often use stainless steel. They are often coated with Alloy625 overlays. Therefore, in recent years, the sales of INCONEL 625 sheets and welding wires have surged.
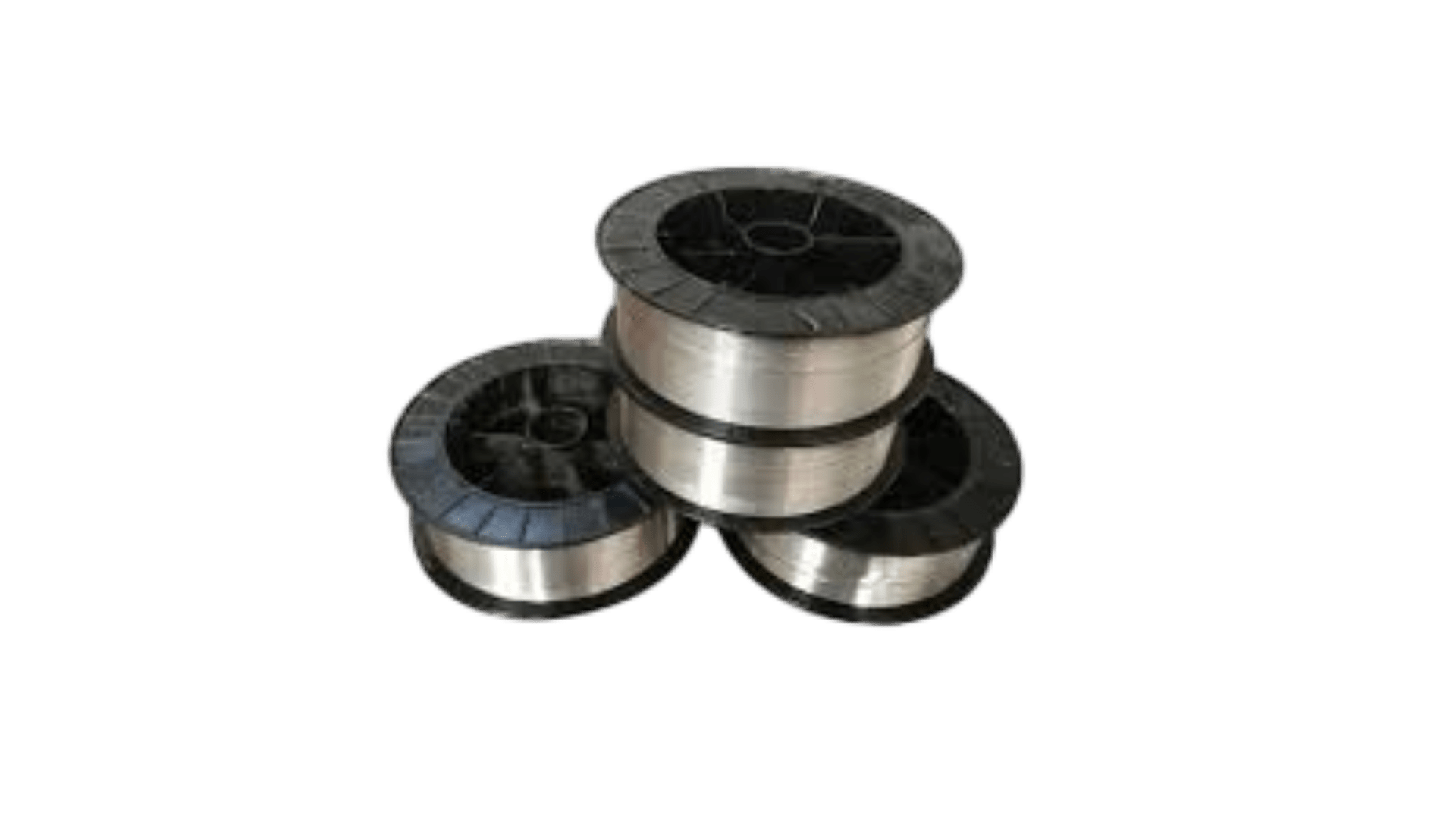
Comparison of INCONEL 625 with Other Inconel Alloys
• INCONEL 625 vs. INCONEL 600
Composition and Properties:
INCONEL 625: Main components include nickel (at least 58%), chromium (20-23%), molybdenum (8-10%), and niobium (3.15-4.15%).
INCONEL 600: Main components include nickel (72%), chromium (14-17%), and iron (6-10%).
INCONEL 625 controls the composition of sulfur and phosphorus better. This gives it improved resistance to intergranular precipitation and creep. The molybdenum content in 625, with its larger molecules, provides higher strength after solution strengthening. The arrangement of chromium and cobalt content in 625 also enhances its mechanical strength.
Overall, alloy 625 costs more than 600. However, it provides better resistance to high-temperature corrosion and is easier to work with when hot. This makes it a better choice for complex structures.
Therefore, 625 is used more often in the international market than 600. This includes pipes, tubes, pipe fittings, sheets, and welding wires.
• INCONEL 625 vs. INCONEL 718
Composition and Properties:
INCONEL 625: Main components include nickel (at least 58%), chromium (20-23%), molybdenum (8-10%), and niobium (3.15-4.15%).
INCONEL 718: Main components include nickel (50-55%), chromium (17-21%), iron (18.5%), niobium (4.75-5.50%), and molybdenum (2.80-3.30%).
Applications: Compared to other materials, 625 is better for high-temperature corrosion-resistant environments. Its strong mechanical strength is useful in marine processing equipment, chemical pipelines, and aerospace parts. The main use is for its corrosion resistance.
Experts recognize INCONEL 718 for its high strength and resistance to deformation at high temperatures. This makes it a good choice for turbine and jet engine parts in aerospace equipment.
These comparisons show that INCONEL 625 is great at resisting corrosion. In contrast, INCONEL 718 is better for high-temperature strength and creep resistance. INCONEL 600 strikes a balance between high-temperature stability and corrosion resistance, suitable for various industrial applications.
Although many people widely use INCONEL 625, other Inconel alloys, such as INCONEL 718, also offer unique advantages. Engineers often use INCONEL 718 in projects that need better mechanical performance because it has a higher yield strength.
INCONEL 718 has a density similar to INCONEL 625. However, its hardness and other properties can change based on specific needs. People particularly know INCONEL 718 for its excellent fatigue resistance, and manufacturers widely use it in aerospace and gas turbine applications.
Conclusion
In summary, INCONEL alloy 625 is a special material. It has high strength and great resistance to corrosion. It can also handle extreme temperatures.
Its chemical makeup and material properties make it suitable for many tough applications. These include aerospace, marine, and chemical processing industries. Understanding the composition and properties of INCONEL 625 helps in selecting the appropriate material for specific applications, ensuring reliability and performance in harsh environments.
INCONEL 625 is available in various product forms, including:
Pipes and Tubes
Plates and Sheets
Bars
Forgings
Wires