Introduction to Nickel Alloy 718
Inconel 718 (Alloy 718, UNS N07718) is a strong nickel-chromium alloy. It is made for high-temperature and high-strength uses. Experts recognize this superalloy for its great mechanical properties.
It has high yield strength and excellent resistance to oxidation and corrosion. It also performs well in extreme conditions. This alloy is one of the most used alloys in industries like aerospace, nuclear, and chemical processing. Essential for making important parts like turbine blades, engine parts, and pressure vessels.
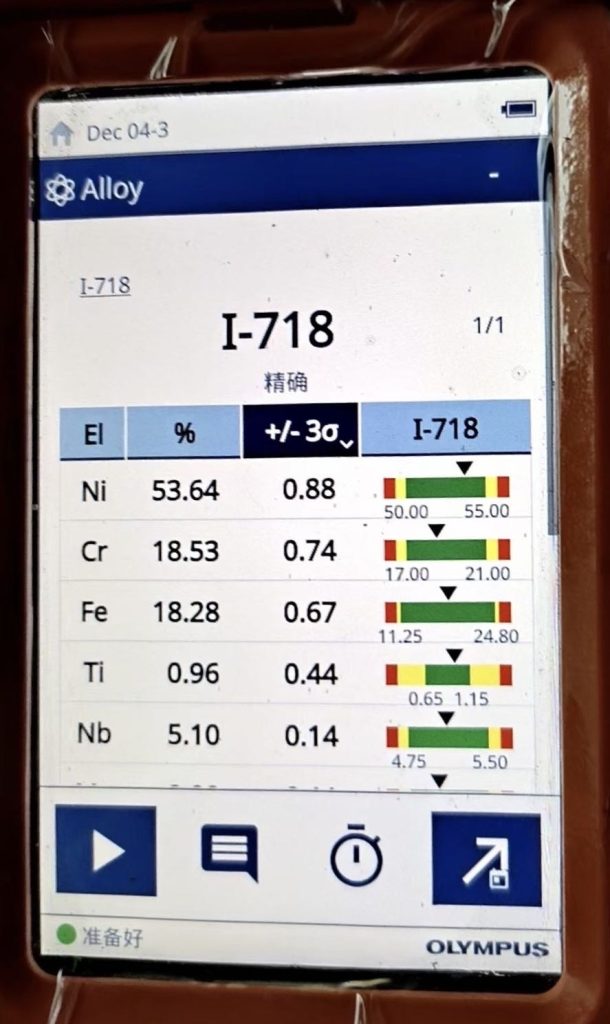
1. Chemical Composition of Alloy 718
Alloy718 is mainly made of nickel (50–55%), chromium (17–21%), and iron. It also contains small amounts of niobium, molybdenum, aluminum, titanium, and cobalt. This mix of elements gives 718 Inconel its strong ability to resist heat and corrosion.
Alloy 718 has a specific composition set by several technical standards. These include AMS 5663, ASTM B637, and AMS 5596.
Element | Contents |
---|---|
Nickel (Ni) | 50–55% |
Chromium (Cr) | 17–21% |
Iron (Fe) | Balance |
Niobium (Nb) | 4.75–5.5% |
Molybdenum (Mo) | 2.8–3.3% |
Aluminum (Al) | 0.2–0.8% |
Titanium (Ti) | 0.65–1.15% |
Cobalt (Co) | 1.0–2.0% |
2. Properties of Inconel 718
2.1 Mechanical Properties of Alloy 718
Alloy 718 is characterized by its high yield strength, high tensile strength, and excellent fatigue and thermal-fatigue strength. These features make it good for use in extreme environments. In these places, parts face high pressures and temperatures.
The alloy’s yield strength can reach up to 130,000 psi (896 MPa), and its tensile strength can exceed 160,000 psi (1,100 MPa) at room temperature. The alloy’s hardness typically falls within the range of 35–40 HRC, but this can vary depending on the specific heat treatment process used.
- Melting temperature of Inconel 718: 1260–1330°C (2300–2430°F)
- Density: 8.19 g/cm³ (718 Inconel density)
- Melting point: Approximately 1330°C (2426°F)
- Hardness of Inconel 718: Can be processed to achieve varying hardness, often falling between 35–40 HRC
2.2 Corrosion Resistance of Alloy 718
One of the main benefits of Alloy 718 is its strong resistance to oxidation, scaling, and corrosion. This is especially true in harsh environments, like those with acidic and chloride-rich substances. The alloy is very resistant to stress-corrosion cracking. It is also great for use in high-temperature and high-pressure settings.
2.3 Thermal Properties of Alloy 718
Inconel 718 keeps its strength at high temperatures. This is important for gas turbines and other industries that use heat. The material can resist creep deformation.
It stays strong at high temperatures. This makes it ideal for the aerospace industry. This is especially true for gas turbines, where parts face constant temperature changes.
3. Applications of Alloy 718
Alloy 718 is commonly used in the aerospace, nuclear, and chemical industries, particularly for components such as:
- Turbine blades and engine parts in jet engines
- Rocket motor components and high-speed aircraft parts
- Pressure vessels and reactor cores in the nuclear industry
- Chemical processing equipment such as valves, pumps, and heat exchangers
- High-temperature exhaust systems in gas turbines and engines
Its resistance to heat, corrosion, and mechanical stress makes Alloy 718 an excellent choice for these demanding applications.
4. Inconel 718 Processing and Manufacturing
The production of Inconel 718 is a specialized process. It changes raw materials into a strong nickel-based superalloy. Engineers use this superalloy in important areas like gas turbines, rocket engines, and aerospace parts.
The process includes choosing materials carefully, using precise smelting techniques, and casting into different shapes. It also involves advanced heat treatment to improve the alloy’s strength and durability.
Inconel 718 comes in many forms. These include sheet, plate, tube, wire, and pipe. This variety meets the needs of industries that need strong, corrosion-resistant, and temperature-resistant materials.
4.1 Inconel 718 Raw Material and Smelting Process
The first step in the manufacturing of alloy 718 is the careful selection of high-purity raw materials. These materials include nickel (Ni), chromium (Cr), iron (Fe), niobium (Nb), molybdenum (Mo), and titanium (Ti). Suppliers around the world provide them, and experts refine them to ensure their purity.
Once the team selects the raw materials, they undergo the melting process. Initially, manufacturers use Electric Arc Furnaces (EAF) to melt the alloying elements together. This method can add impurities. To fix this, we use Vacuum Induction Melting (VIM).
This process happens in a controlled vacuum or inert atmosphere. The VIM process helps ensure that the alloy maintains its purity by preventing oxidation and other contaminants.
After VIM, the alloy often undergoes Electroslag Remelting (ESR), a secondary refining process that improves the uniformity and purity of the material. In ESR, the molten metal passes through an electrically heated slag pool, removing gases, sulfur, and other impurities. This mix of VIM and ESR makes sure that the final Inconel 718 alloy has the strong mechanical properties needed for tough jobs. It includes high corrosion resistance and strength at high temperatures.
4.2 718 Inconel Comes in Different Forms: Sheet, Plate, Tube, Wire, and Pipe
After melting, refining, and casting Alloy 718 alloy, it is available in different shapes for various industrial uses. These forms include:
- Inconel 718 Sheet: Thin, flat pieces of alloy 718 used in applications that require precise cutting, welding, or forming. Manufacturers often use Inconel 718 sheets to make parts like gas turbine blades and heat exchangers.
- Inconel 718 plate is thicker than sheet metal. People use it in areas that need strength and durability. This includes structural components and heavy-duty parts in aerospace and industrial settings.
- Inconel 718 Tube: Hollow, cylindrical forms of 718 Inconel that are ideal for use in high-pressure systems. Industries such as aerospace and chemical processing extensively use these for components like piping and tubing.
- Inconel 718 Wire: Thin strands of alloy 718 used in fasteners, springs, welding applications, and more. Manufacturers also use the wire form to create components for medical devices, aerospace, and other high-performance industries.
- Inconel 718 pipe serves well in tough situations. It can handle high temperatures and pressure. This makes it ideal for the energy and chemical processing industries.
Manufacturers design each type of 718 Inconel to meet strict industry standards. These include AMS 5663, ASTM B637, and other specifications. This ensures the alloy keeps its excellent mechanical and thermal properties.
4.3 Heat Treatment of Alloy 718
After the workers shape the alloy, they subject it to important heat treatment processes. These processes improve its mechanical properties.
Heat treatments are important for Alloy 718. They help improve its strength and hardness. They also enhance fatigue resistance. Overall, these treatments boost performance at high temperatures.
- Solution Annealing: In the solution annealing process, The 718 is heated to about 1,080°C (1,976°F). This helps to make its microstructure uniform. This step helps dissolve any solid particles. It also spreads the alloying elements evenly in the material. This prepares the material for the next stage.
- Aging Treatment: Heat the alloy to about 720°C (1,328°F). This process creates small gamma prime (γ’) particles. This aging process is vital for enhancing the material’s yield strength, tensile strength, and creep resistance. The fine particles that form during aging greatly affect the alloy’s performance. This makes it good for high-stress and high-temperature uses. These uses include gas turbines, aerospace applications, and rocket engines.
Heat treatment processes are important for changing cast Inconel 718. This makes it an alloy that can handle extreme conditions. It provides great performance in industries where strength and resistance to corrosion are crucial.
5. Inconel 718 vs. Other Nickel Alloys
Researchers often compare Alloy 718 to other nickel-based alloys. These include Inconel 625 and Inconel X-750. This is because they all have similar high-temperature abilities.
Inconel 718 has strong yield strength and good fatigue resistance at high temperatures. For example, Inconel 625 works well in areas that need protection from corrosion and oxidation. However, it is not as strong as Inconel 718 in high-stress and high-temperature situations.
6. Sourcing Alloy 718: Suppliers and Distributors
Many suppliers offer Alloy 718. This includes well-known companies like Standard Alloys Inc. and others that focus on high-performance alloys. These suppliers provide Inconel 718 tubing, turnings, and bar stock. They meet the specific needs of different industries.
Southerly Alloy Co.,Ltd. is one of the main suppliers of inconel 718 products. We make sure that the material meets strict international standards. These include ASTM B637, AMS 5663, and AMS 5596. This ensures that the alloy has the right quality and performance.
7. Conclusion
Inconel 718 is a strong and versatile nickel alloy. Industries that need high-strength and high-temperature materials widely use it. Whether for aerospace, nuclear, or chemical processing, Inconel 718 offers superior mechanical properties, corrosion resistance, and thermal stability.
Inconel 718 comes in different forms, like sheets, wire, and pipes. This variety helps it meet the tough needs of industries around the world. As technologies continue to evolve, Inconel 718 will remain a critical material for the most demanding applications.