1. Introduction to Inconel Metal
1.1 Define Inconel
Inconel is a trademarked name for a family of superalloys primarily composed of nickel, chromium, and iron, with additional elements such as molybdenum, aluminum, and titanium. These alloys are known for their excellent resistance to heat, corrosion, and oxidation, making them essential in applications that involve extreme environments.
1.2 What is Inconel?
Inconel refers to a group of high-performance alloys that retain their strength and resistance to oxidation even under high-temperature conditions. The name “Inconel” is synonymous with durability and is widely recognized in industries such as aerospace, power generation, and chemical processing.
2. What is Inconel Metal Made Of?
2.1 Inconel Composition
Inconel alloys are primarily based on nickel, with varying amounts of chromium, iron, and other elements. The exact composition depends on the specific grade of Inconel. For example, Inconel 625 consists of 58% nickel, 20% chromium, 9% molybdenum, and trace amounts of titanium, aluminum, and niobium. This composition provides Inconel with exceptional resistance to high-temperature oxidation and corrosion.
2.2 Inconel Chemical Composition
Different grades of Inconel are tailored for specific applications by varying the chemical composition. Inconel 718, for example, contains nickel, chromium, iron, and significant amounts of niobium and molybdenum, offering outstanding high-temperature strength and resistance to corrosion. This allows for its widespread use in turbine engines and other critical components.
3. Melting Temperature and Point of Inconel Metals
Inconel Alloy | Main Composition | Melting Point Range |
---|---|---|
Inconel 625 | 58% Ni, 20% Cr, 9% Mo, Ti, Al, etc. | 1,300°C - 1,350°C (2,372°F - 2,462°F) |
Inconel 718 | 50-55% Ni, 17-21% Cr, 4.75-5.5% Mo, 2.8-3.3% Nb | 1,320°C - 1,340°C (2,408°F - 2,443°F) |
Inconel 600 | 72% Ni, 14-17% Cr, 8-10% Fe | 1,300°C (2,372°F) |
Inconel Melting Temp / Inconel Melting Point
One of the defining characteristics of Inconel is its ability to withstand extreme temperatures without losing its structural integrity. The melting temperature of Inconel alloys varies depending on the grade. For example, Inconel 625 has a melting point of around 1,300°C (2,372°F), while Inconel 718 melts at approximately 1,320°C (2,408°F). These high melting points make Inconel alloys ideal for use in high-temperature environments such as jet engines, gas turbines, and other applications where metals are exposed to heat for extended periods.
4. What is Inconel Used For?
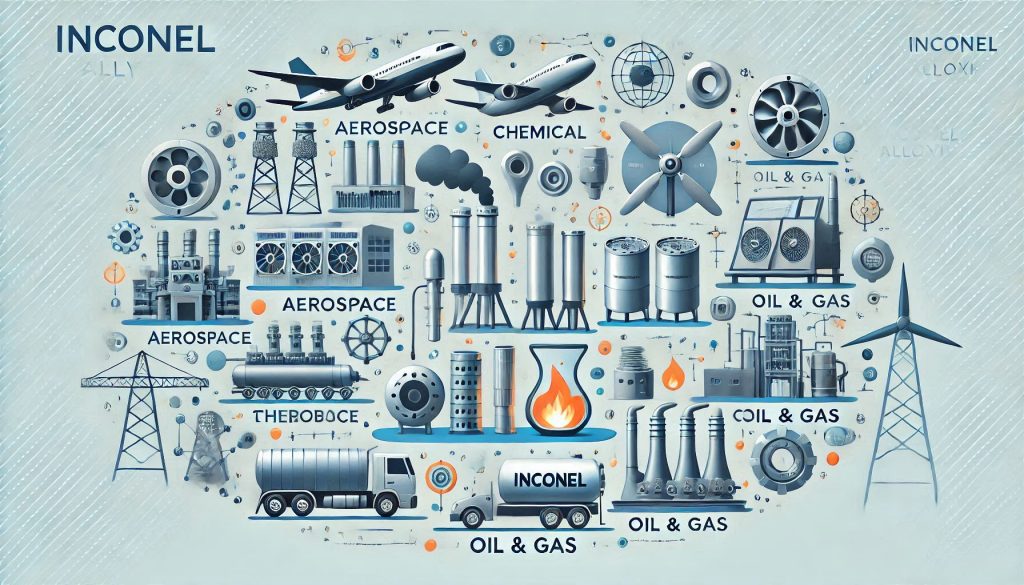
4.1 Inconel Metal
Industries that require materials to perform under high heat, pressure, and corrosive conditions extensively use Inconel. Some of the most common applications include:
- Aerospace: Inconel is commonly used in aircraft engines, turbine blades, and exhaust systems. It is strong at high temperatures and resists oxidation.
- Chemical Processing: The chemical industry uses Inconel alloys in reactors, heat exchangers, and pipes. People choose them for their resistance to corrosive substances.
- Power generation relies on Inconel for gas turbines and nuclear reactors. It can handle high pressures and temperatures, which is crucial.
4.2 Inconel Alloy
Inconel’s versatility is evident in its application across various sectors. A key material in industries that need strength at high temperatures is present. It also resists corrosive environments. This makes it perfect for high-performance uses where failure cannot happen.
5. Inconel Grades and Variants
5.1 Inconel Grades
Inconel alloys come in various grades, each suited to different performance needs. Common grades include:
- Inconel 625: Known for its excellent fatigue and thermal-fatigue strength, as well as its outstanding resistance to oxidation and corrosion.
- Inconel 718: Offers superior tensile and yield strength at high temperatures, ideal for jet engine components.
- Inconel 600: Known for its resistance to oxidation in high-temperature environments, particularly in industrial applications.
5.2 Inconel X
Engineers use Inconel X, a lesser-known variant, in specialized high-temperature applications. It provides a good balance of strength and corrosion resistance, particularly in gas turbines and other high-performance machinery.
6. Inconel vs Other Materials
6.1 Inconel vs Steel
While people often compare Inconel to stainless steel, it outperforms traditional steels in extreme environments. Stainless steel has good resistance to corrosion but cannot handle the same high temperatures as Inconel alloys.
Inconel can keep its strength at high temperatures. It also resists oxidation exceptionally well. This makes it a great choice for aerospace, chemical processing, and power generation.
6.2 Inconel vs Other Materials
Inconel is better than materials like titanium and aluminum alloys. It resists oxidation well. It also keeps high strength and works well in extreme heat changes. Its superior properties at high temperatures make it indispensable in fields that demand the highest levels of performance.
7. Performance and Properties of Inconel
Inconel Meaning
Inconel’s significance lies in its ability to perform under the most demanding conditions. Its combination of strength and durability makes it a reliable material. It can resist high heat and corrosion. This makes it suitable for tough environments.
Engineers design Inconel alloys for high performance. They keep their strength and resistance to fatigue, even at extremely high temperatures.
8. Inconel Manufacturing and Processing
Manufacturers typically produce Inconel alloys through casting, forging, and welding processes, often requiring specialized equipment because of their toughness. The material is hard to machine. This requires careful handling and special cutting tools. Advances in manufacturing technologies, such as additive manufacturing (3D printing), are improving the ability to create Inconel components more efficiently.
9. Conclusion
Inconel alloys are an essential material for modern industries that demand reliability under extreme conditions. Inconel is important in many fields, from aerospace to chemical processing. It helps create high-performance technologies.
Inconel has special properties. It has a high melting point and resists oxidation. It also stays strong at high temperatures. These features make it useful in tough industries.
As industries advance in technology, the need for materials like Inconel will increase. This will make it essential for engineering solutions in the future.